
Technology & Development
The X-WAVE shaft has a double structure braided with multiple strands of high-modulus carbon fiber from the tip to the butt to compensate for the shortcomings of the typical manufacturing method.
Background
Limitations of common shaft manufacturing methods
- To develop the strength and torque of the shaft by using the carbon fiber prepreg sheet, which is the raw material for manufacturing the shaft, sheet (4) with carbon fibers arranged in the total length direction, and sheet (3) with carbon fibers arranged in the diagonal direction are rolled in several layers.
- Rolling technology is used by adding a small reinforcing sheet to reinforce the strength of the tip and adjust the kick area.

Structural analysis of elastic behavior according to the swing mechanism of the shaft

Common carbon fiber Graphite Golf Shaft material composition and manufacturing process
At the top of the driver's backswing, the head falls slightly lower than the axial direction of the shaft due to the inertia of the head weight.
When you accelerate the shaft while swinging down, the gravity and inertia of the head cause the shaft to bend to the right and upward, in the opposite direction of the swing. The actual force acting on the shaft is a three-dimensional complex combination of right-to-left force and top-down force acting on the entire shaft.
The curved shaft causes the head to hit the ball slightly forward (Lead Deflection) or downward (Toe Down Deflection) at the moment of impact due to the elasticity that returns to the original position according to the designed elastic strength (Flex) and the acceleration force due to the weight of the head.
A torque is applied to the shaft due to the rotation of the driver head, and the head is aligned (open/closed) at impact due to the difference between the head's center of gravity and the shaft's central axis or the rotation of the left and right wrists during the entire swing process.
Shortcomings of the rolling method carbon fiber graphite golf shafts
- A shaft that is more flexible (low flex) compared to the swing speed generates more lead deflection and toe down deflection at impact. As the shaft is pulled, the head face closes (in severe cases, a bad hook ball) or the golf ball hits the upper part of the head face, increasing its trajectory and resulting in a shorter distance.
- A shaft that is stiffer (higher flex) than the swing speed does not reach the appropriate Lead Deflection and Toe Down Deflection amounts at impact. When the head face is open (in severe cases, a slice ball) or the golf ball is hit at the bottom of the head face, the trajectory is lowered and the distance is shortened.
- The difference in the degree of Lead Deflection and Tow Down Deflection due to swing speed and shaft flex is due to the difference in the elastic action of the carbon fibers arranged on the shaft that act during the swing process. Among the carbon fibers arranged on the shaft, those arranged in the direction opposite to the bending of the shaft have an elastic effect, but those arranged in the bending direction do not.
- Rolling technology is applied to prepreg sheets with carbon fibers arranged diagonally to reinforce elasticity.
- The prepreg sheet with carbon fibers arranged diagonally has a limit to the elasticity acting on the shaft because the carbon fibers are positioned in a broken form at a certain length.
- Due to the dynamic movement caused by shaft swing and the structural limitations of the carbon fiber prepreg sheet, general graphite shafts have difficulty hitting the ball accurately due to rapid changes in swing speed. It is challenging to create consistent pitches when a golfer using the R-Flex swings at different speeds depending on their condition or desire to swing.
- Various shaft manufacturing companies use the following technologies to compensate for the above problems: A thin carbon fiber prepreg sheet in the form of tape is wrapped diagonally around the entire shaft (TPT), manufacturing method using prepreg sheets woven with carbon fiber (Seven Dreamers), winding technology (PEDERSON) that winds carbon fiber strands around a shaft in a spiral shape at different angles, etc.
Manufacturing Technology of X-WAVE
The X-WAVE shaft has a double structure braided with multiple strands of high-modulus carbon fiber from the tip to the butt to compensate for the shortcomings of the typical manufacturing method.
01
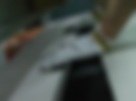
Multiple strands of composite carbon fiber wire are braided seamlessly from the tip to the butt to strengthen the elasticity and resilience against bending and twisting in all directions of the shaft.
02

By arranging the rolling and braiding layers of the shaft in various ways or applying different numbers of filaments and weaving strands of the braided carbon fiber, shaft manufacturing technology with various characteristics is secured.

In terms of the mechanism of the golf swing, braided carbon fiber acts elastically in the direction opposite to the direction in which the shaft bends, while simultaneously supporting the shaft in the direction of bending. No matter what speed the shaft is swung, a balanced force is applied to the direction of the force that drops the swing and center shaft down and the force that swings from right to left, always returning to the original position.
03

Swing Robot
Comparison Test

Typical rolling fabrication shaft
X-WAVE Braiding Shaft
The 50g R-Flex shaft manufactured using the general rolling method flies straight when the swing speed is 88mph. However, when the swing speed is increased to 95 mph or 100 mph, the head face is gradually closed, resulting in a pitch that hooks to the left of the target direction.
VS
The 50g range shaft manufactured using X-WAVE's braiding method has little change in the head face angle at impact even if the swing speed is increased to 88 mph, 95 mph, or 100 mph. It achieves the best carry distance while implementing an appropriate launch angle.
Patents and Certification Materials

Technical data and papers of X-WAVE Golf shafts
1) Seamless carbon fiber golf shaft manufacturing design
Gwangbo Shim, Bongam Choi Korean Golf Association/ 2014.7.3. No. 1
2) Relationship between golf ball dynamics and human characteristics during driver swing according to golf shaft characteristics
Journal of the Korean Society of Sports Science, written by Choi Bong-am and 3 others, September 30, 2016. No. 25-5
3) Characteristics of golf shafts produced by carbon and basalt fibers
Journal of Ceramic Processing Research (SCI) Choi Bong-am and 7 others
4) Analysis of differences in distance and direction by drive shaft strength
Choi Bong-am and 2 others Journal of the Korean Golf Association 2014.6.30. Volume 8, Issue 2
5) Task designated by the Ministry of Culture, Sports and Tourism (personally customized golf club shaft manufacturing design using cutting-edge new materials)
(Assignment number 1375025972 Technology field HE1399)
6) Patent application 10-2022-0076505 Golf club shaft manufacturing method FBT Co., Ltd. and 1 person (Choi Bong-am)